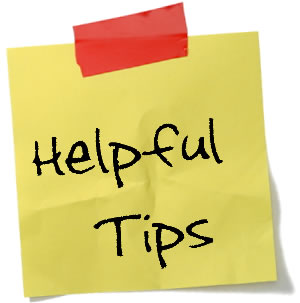
For my Facebook fans you already know about this great feature. But for those of you that are not connected to A Lean Journey on Facebook or Twitter I post daily a feature I call Lean Tips. It is meant to be advice, things I learned from experience, and some knowledge tidbits about Lean to help you along your journey. Another great reason to like A Lean Journey on Facebook.
Here is the next addition of tips from the Facebook page:
Lean Tip
#3631 – Embrace Uncertainty
Change
often brings uncertainty, and embracing uncertainty is key to adaptability.
Accept that change is inevitable, and that uncertainty is a natural part of
life. Instead of resisting or fearing uncertainty, develop resilience and learn
to thrive in the face of the unknown.
To
embrace uncertainty, practice mindfulness and focus on the present moment.
Cultivate a sense of curiosity and openness to new experiences. Remind yourself
that uncertainty can lead to growth and new opportunities. The more you embrace
uncertainty, the more adaptable you will become.
Lean Tip
#3632 – Seek New Experiences
Stepping
out of your comfort zone and seeking new experiences is another way to embrace
change and develop adaptability. Engaging in diverse activities and exposing
yourself to different perspectives can broaden your horizons and expand your
ability to adapt.
To seek
new experiences, challenge yourself to try something new regularly. It can be
as simple as trying a new hobby, exploring a different neighborhood, or
engaging in a new social activity. The more you expose yourself to new
experiences, the more adaptable you will become.
Lean Tip
#3633 – Ask “What If” Questions to Push Boundaries
If you
want to help your team, be bold and innovative, ask questions that push them to
think outside the box. Don’t limit your questions to slight modifications of
the status quo. Ask questions that probe current boundaries and limitations. As
a result, your team will start to think innovatively. You can ask questions
like: “What if we had to build this process from scratch? What would we do
differently?” or “What if our main product suddenly became obsolete?”
Such
questions may seem far-fetched, but they prepare you to handle sudden
disruptions. And often, the seemingly absurd happens think about how many
industries saw their main products become obsolete thanks to the pandemic
disruption! Asking these hypotheticals encourages your team to expect the
unexpected, think creatively, and respond to uncertainty on their feet. You can
do this in team brainstorming sessions and also in one-on-one meetings.
Lean Tip
#3634 – Change Your Mindset, Focus on Continuous Improvement
One of
the biggest ways manufacturers can learn to deal better with change is to
become an organization that embraces a culture of continuous improvement.
Manufacturing companies that focus on continuous improvement are not only more
likely to succeed in an ever-changing business environment, but they are also
more likely to implement changes when needed.
This type
of company culture prioritizes continually making small changes that improve
operational processes. It involves constantly reviewing processes and
procedures, looking for ways to make them more efficient and effective. It’s
important to encourage feedback from employees at all levels of your
organization and to use this feedback to make meaningful changes.
If your
staff is always focused on making improvements and changes — and is included in
the change-making process — they will naturally become more comfortable with
change over time.
Lean Tip
#3635 – Invest in Training and Development
To
embrace change you must invest in training and development for your employees.
This includes providing access to training programs, workshops, and seminars
that help employees stay up-to-date with the latest trends and technologies.
It’s important to create a learning culture where employees are encouraged to
learn and develop new skills.
In
addition to providing training opportunities, it is also important to recognize
and reward employees who actively seek out opportunities for learning and
development, as this reinforces a culture of continuous improvement, encourages
ongoing professional growth and makes staff more open and comfortable with
change.
Lean Tip
#3636 – Address Continuous Improvement Challenges By
Communicating Openly
The most
important thing you can do when introducing anything new into your business is
to communicate with your employees as to the reason why. By clearly
communicating the need for process improvement and process improvement tools,
you can help to reduce fear and actually spark interest/ support.
Lean Tip
#3637 – Address Continuous Improvement Challenges With A Proof-of-Concept
Rather
than starting with widespread alterations, you can begin with a
proof-of-concept project. For example, if there are multiple processes you wish
to amend, start with one.
Then, you
can use it as an example as to how the no-code tool has not only improved the
organization, but also the lives of employees, too. When employees experience
the benefits first-hand, they will be more willing to take part in widespread
changes.
Lean Tip
#3638 – Make Continuous Process Improvement the Norm Within Training
Change
isn’t always easy. It’s vital to train and support employees as you make any
adjustments to existing processes. This is especially true when you implement
new technologies and want your employees to make use of such tools. They should
feel comfortable using new technologies as part of their processes and
routines.
Lean Tip
#3639 – Improve Your Process with Time Studies
One of
the most significant resources wasted within a business is time. Being able to
accurately measure and gauge how much time a process takes on behalf of your
employees can offer insight into where you can optimize a process. It’s as
simple as using software to time a process. Then, you can analyze how long
processes take and find ways to eliminate wasted time. This could be in the
form of automating approvals and reducing touch-points, thereby preventing
potential bottlenecks and delays from occurring.
Lean Tip
#3640 – Use Catchball to Get Continuous Improvement Going Within Your Organization.
Within
organizations, processes are rarely started and completed by a single person.
As such, every process needs to have someone who can be held responsible for
its execution, but still requires the input and assistance of multiple people.
Catchball is a method of continuous improvement that requires the person who
initiated a process to state its purpose and concerns to the others involved
clearly. In this way, they can then “throw” it out to the group for feedback
and ideas for improvement, yet the single person remains responsible for its
completion.
Lean Tip
#3641 – Emphasize a Personal Understanding of the Philosophy of Kaizen Across
all Levels of the Organization.
Instilling
an understanding of kaizen as a long-term practice, rather than a management
initiative, is important in order to sustain continuous improvement. Continuous
improvement is as much about mindset as it is about actions.
Making
sure your employees understand the history and philosophy of kaizen will help
sustain a culture of continuous improvement that permeates the company.
Building a company culture with a steady focus on improvement is critical to
maintaining momentum in your kaizen efforts.
Lean Tip
#3642 – Empower Your Employees to Solve Problems
Employees
who are closest to the problems in your operations are the best-equipped to
solve them. They are your greatest assets in your kaizen efforts, so give them
the support they need to implement improvements. Developing your team’s
abilities through training and support should be as much a part of your
continuous improvement program as making improvements to manufacturing
processes.
Additionally,
engaging team members to identify problems and suggest improvements in their
work areas encourages a sense of ownership over their work, which can improve
overall motivation, morale, and productivity.
Lean Tip
#3643 – Document Your Process and Performance Before and After Improvements
have Been Implemented
In
kaizen, it’s important to “speak with data and manage with facts.” In order to
evaluate improvements objectively, existing procedures must be standardized and
documented. Mapping the process’s initial state can help you identify wastes
and areas for improvement and provide a benchmark for improvement.
Measuring
performance against existing benchmarks allows you to demonstrate ROI from your
kaizen efforts and keep the company aligned around improvement. It also allows
you to identify areas where your efforts are working–or not–so you can make
strategic decisions about future improvements.
In order
to measure performance objectively, you should identify metrics that quantify
improvements. These may include metrics revolving around quality, cost,
resource utilization, customer satisfaction, space utilization, staff
efficiency, and other KPIs.
Lean Tip
#3644 – Standardize Work to Make Improvement Last
In order
for improvements to last, they must be standardized and repeatable.
Standardizing work is crucial to kaizen because it creates a baseline for
improvement. When you make improvements to a process, it’s essential to
document the new standard work in order to sustain the improvements and create
a new baseline. Standard work also reduces variability in processes and
promotes discipline, which is essential for continuous improvement efforts to
take root.
Lean Tip
#3645 – Create Your Own Kaizen Guidelines
While
there are many resources available to guide you through your kaizen efforts,
it’s important to personally understand your company’s kaizen journey.
Reflecting on your kaizen efforts after improvements have been implemented is
an important part of the continuous improvement cycle.
As you
reflect on your efforts, develop your own kaizen guidelines. Start by creating
guidelines based on your own experiences improving the workplace. Keep in mind
that these guidelines should be for your colleagues, your successors, and
yourself to understand the problems you have overcome. These guidelines will
ultimately help you as you approach your next challenge.